Lithium batteries are among the most widely used rechargeable batteries in the world, and their popularity continues to grow due to their high energy density, long lifespan, and low self-discharge rate. Lithium-ion batteries, in particular, have become the choice for many applications, from smartphones to electric cars.
Despite their many benefits, however, lithium batteries do come with some risks, especially when they are not manufactured properly. Safety is a top priority when it comes to their production, and ensuring quality and reliability is essential in preventing accidents and ensuring their long-term performance.
One type of lithium battery that has gained popularity in recent years is the 32650 liFePO4 battery. This battery is a cylindrical cell that is often used in electric vehicles, solar energy storage systems, and other applications that require high-power output and long cycle life. Like other types of lithium batteries, however, they must be produced with strict quality control measures to ensure their safety and reliability.
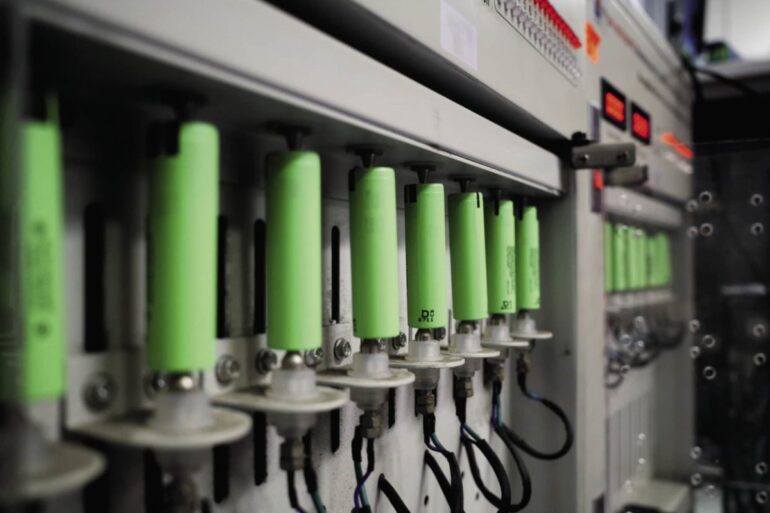
One of the most important aspects of lithium battery production is the quality of the raw materials used. The materials that make up its electrodes, electrolyte, and separator must all be of high quality and purity to prevent contamination and ensure consistent performance. In addition, the manufacturing process must be carefully controlled to prevent defects and inconsistencies that could compromise its safety or performance.
Another key factor is the design of the battery itself. The 32650 liFePO4 battery, for example, is designed to be more stable and less prone to overheating or exploding than other types of lithium batteries. This is because it uses a cathode material made of lithium iron phosphate (LiFePO4), which is less reactive than the cobalt-based cathodes used in many other types.
Despite this inherent stability, the battery must still be designed and manufactured with safety in mind. This includes ensuring that its electrodes are properly aligned, that the electrolyte is evenly distributed, and that the separator is of the correct thickness and porosity.
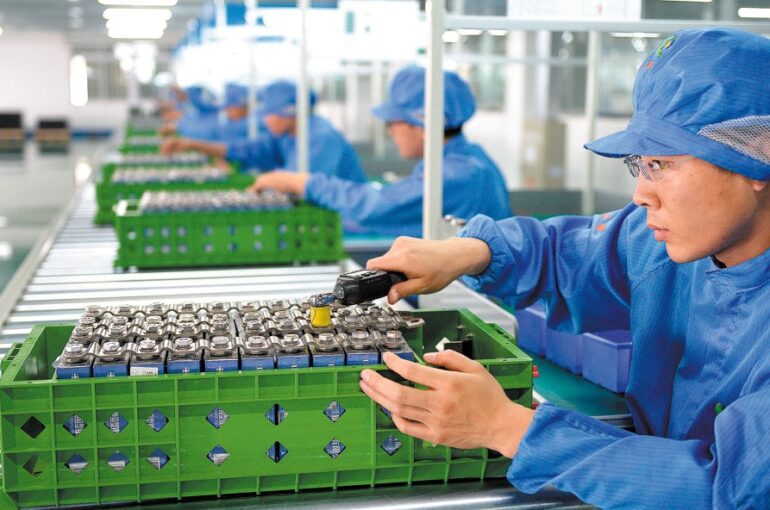
Once the battery has been produced, it must be carefully tested and inspected to ensure its quality and reliability. This includes performing electrical tests to verify that its voltage, capacity, and internal resistance are all within acceptable ranges. In addition, it must be subjected to environmental tests to ensure that it can withstand extreme temperatures, humidity levels, and mechanical stresses without experiencing degradation or failure.
In conclusion, safety is of paramount importance in the production of lithium batteries, including the 32650 liFePO4 battery. Ensuring quality and reliability requires strict control over the quality of the raw materials, the design and manufacturing process, and the testing and inspection procedures used. By following these best practices, manufacturers can help to ensure that their batteries are safe, reliable, and perform well over their entire lifespan. This not only protects the end user from harm but also helps to build trust and confidence in their use as a viable and sustainable energy storage solution.